Hi,
That is very kind of you jj thank you. You are so right; I do my best at everything I attempt or do; it's the way I was taught and will always remain with me. It can be a pain at times because I'm my own worst critic unable to accept near enough is good enough?
I thought I had completed this story but then remembered another little story I can tag on regarding winding. 14 years ago when I first adopted vintage radio restoration as a winter hobby it didn't take long before I had a radio chassis on the bench to play around with; as I progressed I quickly came to realize I needed three hands for chassis work? One hand for the soldering iron; one hand for the solder and one hand to hold the component into position whilst it was being soldered. On items such as valves with large bases where access with a soldering iron was relatively easy it was still quite difficult to replace components leaving them looking neat; on valves with small bases and many pins it was a downright pain trying to solder a new component in without burning lots of adjacent leads etc?
As usual I ended up with a restless night having awoken in the early hours with this problem on my mind; I thought of all kinds of wonderful and weird solutions but by the time I got out of bed I had a working solution which I was keen to try out. I had seen tiny wire coils like miniature springs on a Philip's chassis I had been working on and these tiny coils very neatly had been slipped over a number of leads and soldered leaving a very tidy joint indeed.
What if I could design a small tool to add a miniature coil directly to the end of component leads such as resistors or capacitors; these components usually came with a decent lead length? I searched through my metal offcuts and selected bits of metal in line with what I had in mind. A simple base was cut then drilled and countersunk on centre to accept a countersunk socket 6mm machine screw. A short length of square section BMS bar stock was cut and this was end drilled and tapped at 6mm to accept the machine screw taking care of the base and pillar; the other end was drilled and tapped at right angles to accept a 5mm set screw or socket screw. A short length of thick metal strip was cut and drilled on centre at 5mm clearance this to be the needle/spindle clamp. I did have difficulty deciding how to provide the coil forming spindle this needing to be quite small diameter but tough enough to withstand the stresses involved. I eventually settled on a heavy gauge tapestry needle and bought a packet of these at Hobbycraft whilst searching the store for something suitable. The needles were very cheap. Now for a bit of lathe work; I turned a nice thimble which was to be the spinner and drilled this on axis to accept the needle with a very close tolerance but sliding fit. I used the hacksaw to add a cross slot to accept the wire (lead) to be wound.
It's another of my long rambling experiments but eventually I wound the first miniature coil and it was perfect; such little things really do please me when they come together so well. I added miniature coils to a number of resistors and capacitors also I found it very easy to add miniature coils to the ends of extension wires etc. So the idea actually works in practice; brilliant. What had been such a chore previously now was transformed into very easy task indeed; I removed components one at a time by snipping both wire leads but leaving a short end attached to the chassis about 1/4" long; these short ends were scraped clean with a craft knife then the new component was simply dropped into place over the two short wire ends leaving both hands to solder the component into place. This worked a treat and not only did it give a very neat joint; less heat was required and no adjacent damage was caused; as a bonus the two short ends gave a positive location as to where the new component needed to be installed; previously I found I had to take notes before snipping a component out otherwise it was so easy to lose the locations.
Having designed and proved the miniature winder worked to my satisfaction I had an article published in the British Vintage Wireless Society "Bulletin" giving full construction and usage details and also posted details onto a couple of radio restoration forums where it was very well received in fact I've made a number of these and given them away as gifts; I've been asked by forum members if I would make them a miniature winder and they would be very happy to pay; in each case I quietly made a winder and posted it on with my compliments. These days I've moved onto other projects which fully occupy me.
I find life fascinating and can turn the most mundane task into a very nice interesting project as this miniature wire winder proved to be? I love dreaming up these little jobs then spending ages trying to make them work. I hope this is of interest?
Kind regards, Col.
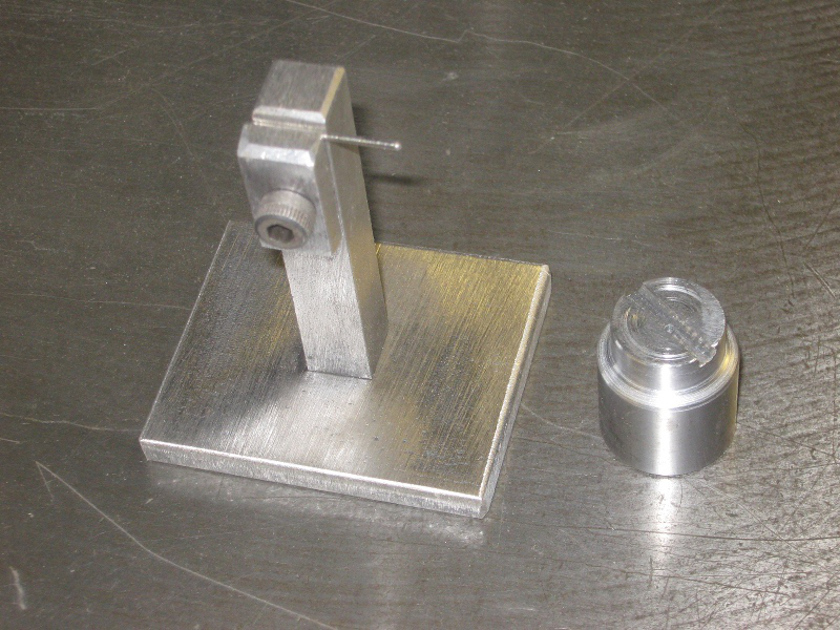
- Wire winder 1..jpg (308.86 KiB) Viewed 1522 times
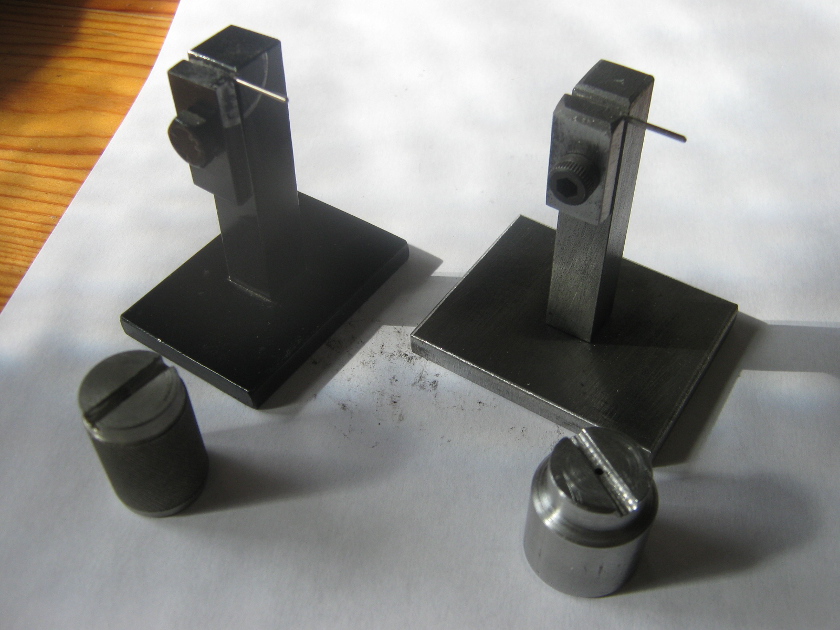
- Pair of winders.jpg (205.97 KiB) Viewed 1522 times
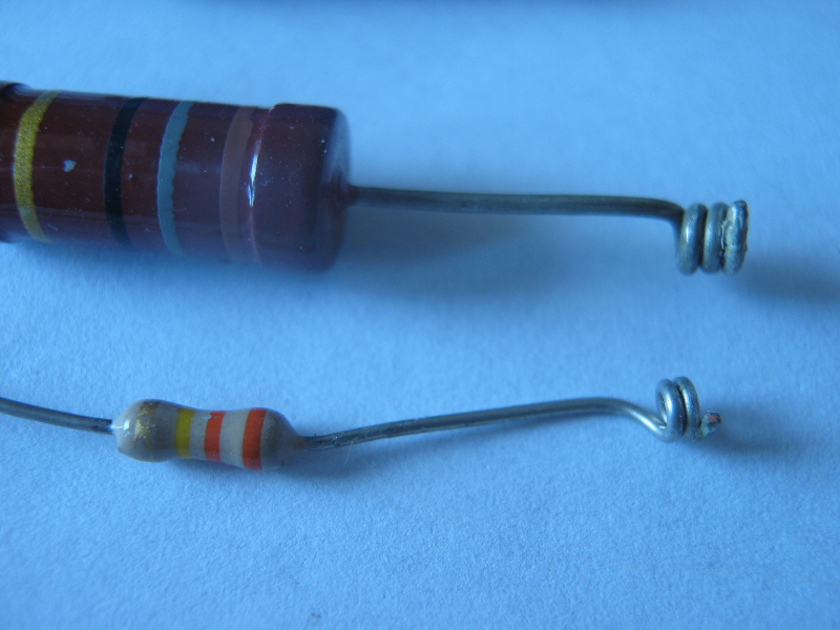
- Sample coils close up..jpg (216.86 KiB) Viewed 1522 times