Hi,
I think I've covered some of the questions asked but I don't mind in the least when it comes to encouraging anyone to adopt new skills and welding is a very useful skill to possess in fact without welding equipment or the skill to use really does limit workshop activities but I'll own up and say I'm totally biased due to welding for over the last 50 years. Please do note I'm not a coded welder and never will be; I was taught both arc and gas (Oxy/Acetylene) welding as an apprentice and ever since my welding jobs have been 99.99% mild steel mostly angle; box/ channel and RSJ plus of course assorted plate. I've never used TIG; MIG or handled an inverter welder so as usual I can only write about what I know works for me. YouTube is brilliant if any member wishes to delve deeper into assorted welding equipment.
One thing I would like to make perfectly clear is that arc (stick) welding IS NOT DIFFICULT to learn. Safety is paramount and I suggest reading up and perhaps viewing a few videos before attempting arc welding for the first time; where electricity is involved water is a definite no no; work in a dry environment and don't hold the electrode with one hand whilst leaning in the earthed work piece. I used to stand on 1" thick plate wearing hob nailed boots in total safety so although please be careful just be aware of the potential for accidents. If you insist on welding near a petrol tank then have the ambulance and fire brigade handy in fact an undertaker would also be useful. Study the safety rules first and understand them then you'll be OK; I'm not trying to put anyone off welding but it would be reckless and remiss of me to simply encourage a pure novice to fire up an arc without understanding basic safety rules.
Right enough said on safety and now you are keen to get welding which I fully understand. Firstly the welder duty cycle;
http://www.zena.net/htdocs/FAQ/dutycycle.shtml
Now to a welder I know and have used for over 20 years with 100% success;
http://cpc.farnell.com/sip/05741/arc-we ... ng-TL19143
My SIP welder was bought new over 20 years ago so hopefully quality hasn't suffered since then but I liked my SIP welder and it was this size at 140A. I note duty cycle isn't quoted but as to duty cycle on my own trusted SIP the duty cycle could be greatly extended by keeping the welding current as low as possible whilst still giving a good strong weld also I paced the welding by setting up the components welding a few then switching the welder off whilst I arranged more components; the welder whilst ever switched on will be generating some heat. Duty cycle I believe is the rating at full amps but lesser amps increases the duty cycle. I believe your welder is 140A Argyll so you're off to a flying start all you really need to do is to stick an electrode in and do some practicing; if only you lived near I could have you welding in no time at all. Shop around for best welder offer the above is only an example.
I would definitely not recommend a cheap Lidl arc welder; a decent 140A welder can be bought for a little more cash and the extra cost will soon be forgotten but replaced by years of reliable welding; I don't know about the very cheap welders but can only guess their duty cycle will be very short although they will I think have an overload included which trips once the welder over heats so to answer this particular question when the welder trips leave it alone for about 30 minutes then it should work as normal again after its cooled down.
You are most welcome Griff84. Congratulations on your career change and choosing mechanical engineering which I'm sure you'll adopt and enjoy for many years yet to come. I'm quite alarmed though because if welding is no longer taught due to H&S regulations we are doomed. I know safety is paramount but I was using big full sized Oxford oil cooled 3 phase welders and BOC Sapphire welding and cutting torches (Oxy/Acetylene) as soon as I was old enough under law at the age of 16 but then we enjoyed real apprenticeships shared between college; training centers and on the job. Certainly no disrespect to fitters but there is a whole world of difference between a mechanical fitter and a mechanical engineer; I was taught the old fashioned way how to be a mechanical engineer and my job description from the start was "Apprentice mechanical engineer" I'm proud to this day to have been considered worthy to be taught as such. Fitters fit whilst engineers can make and fit as seen in many of my threads. I hasten to add I'm no one special the only difference is I was taught to be the way I am and I enjoy sharing my bit of knowledge of which arc welding is a part.
I think too much worry and stress is being placed upon learning to arc weld; the actual arc welding is easy enough what is difficult is getting everything ready to weld especially when it comes to cutting metal in a home workshop; I was brought up with files and hacksaw plus hammer and cold chisel; it's truly amazing what can be achieved with such basic kit but back to welding. Practice on bits of scrap like angle iron and box section with sections 1/8" thick or over; once a bead can be run then you are a welder and more practice will soon see very strong joints; your first weld will possibly look perfect until you whack it with a chipping hammer to remove the slag and reveal the true weld; if the electrode sticks simply release the electrode or quickly turn the welder off.
To strike an arc can be done in two ways; stroke the tip of the electrode along the work or to tap the tip of the electrode; I prefer to tap; the idea is to simply tap the tip of the electrode at the start of the weld but not tap hard; tap to make contact with the metal but immediately the electrode needs to "bounce" clear of the metal by say an 1/8" of an inch; it is this small gap that causes so much trouble; if the electrode is allowed to be in full contact with the metal whilst the supply is switched on then this is nothing more than creating a direct short exactly as if a spanner was placed across battery terminals which I don't recommend either; a direct short is not wanted but the purpose of tapping is to create the current flow; once contact is made then electric current flows but this is the crux of arc welding; consider a sparking plug used in a petrol engine; you know what the spark looks like; sorry if you don't but in welding this spark is the electric current flowing and the spark is now called the arc. Once this very basic information is grasped and the arc can be struck then the small gap between metal and electrode needs maintaining as welding progresses because the electrode is now becoming shorter as the weld is laid; the sound of the welder will guide you in fact once you learn its language it is a very good guide letting you know if the arc is too long or too short; a novice after reading this hopefully will be alert to listening for it; a direct short and the welder will be annoyed. Stroking also creates the arc but better than text please watch a few videos on YouTube to see the arc being struck; Once the arc can be struck and maintained and the bead run in the correct position the welder does the work so time to relax and enjoy sticking bit of metal together; it always fascinates me.
Once the arc can be struck without the electrode sticking then the hard part is over; I have my big oil cooled welder and can still get the electrode to stick so it's nothing to worry about but when it sticks for a novice for the first time panic tends to quickly set in; all it means is that the novice is on a new learning curve; it happened to me and it will happen to any novice welder; its this sticking which strikes fear into a novice at first but after its happened a few times and the novice sees a bright star in his/her eyes this is arc eye; a bad case of arc eye I'm told is like having sand in your eyes but I don't know of anyone suffering permanent eye damage; A WORD OF WARNING BEFORE I FORGET: NEVER EVER ARC WELD IF YOU WEAR CONTACT LENS. I read contact lens can actually weld to the eye.
I can ramble on forever but how hard can arc welding be when I has a kid of sixteen of age could weld RSJ's which was only the tip of what I was being taught? C'mon guys get stuck in play safe but learn to arc weld you'll never regret it; I still enjoy welding to this day; I've even now got my own industrial oil filled welder which trips the 32A mcb but this is another project which I'm resolving very shortly by sorting out the electrics in the bungalow and workshop.
You're entering a fascinating new world Griff84 when it comes to mechanical engineering; I'd love to see you develop your skills allowing you too to design and make your own machinery; it might sound impossible to you at the moment but how many are taught a skill and just stick to what they've been taught; I'll have a go at anything if I find it of interest; safety first though and if I'm new to something which could harm or kill me I do lots of research but then I do the work.
As I say welding is the easy part so I'm happy to show a bit of what is actually involved in welding; the weld is important but so are the parts being welded; welding is only part of an assembly process; I needed to cut multiple lengths of black iron whilst installing a new deck and railings above our garage last year; this is posted elsewhere on the forum but highly relevant here so a few details to encourage anyone to take up welding.
OH dear as I tried to submit I was asked to logon and by doing this lost quite a bit of text; I never learn; I should write using my Microsoft Word and keep "saving" but at least I've saved the above by pasting? I'd better save this before it too disappears.
Here goes again. Welding is only part of a process; the hard part is getting the components ready to be welded not only in accurately cutting to size but in assembling if there are multiple components such as in the new metal railings I designed and made last year. Components to be welded really need to have accurate joints being butted together without big gaps showing; take the new railings; I had the black iron delivered in full lengths at over 20' long so I needed to cut multiple lengths as accurately as I could; I can split a line with an hacksaw but it's hard work; OK for a one off but I needed an easier solution. I have a lathe and a welder and also a 9" angle grinder so I put together an hinged stand turning the angle grinder into a cut off saw with a metal cutting disc installed; this was very basic indeed and I used a block of timber to hold the head of the grinder clear until needed; with a length stop arranged; I donned my ear defenders and quickly cut the lengths all to accurate length well certainly accurate enough for this project. The heavy channel and box I cut freehand using the angle grinder. I dislike angle grinders but in this instance the angle grinder was worth its weight in gold; again safety issues; angle grinders are very dangerous and create huge amounts of sparks that can ignite anything in their path; ear defenders; gloves and eye protection is a must; it's no good looking macho in the A&E who are never impressed.
I keep banging on about accuracy but only because accuracy is so important; once the components are cut then they need arranging in there final position before welding but again a novice is likely to stumble wondering how to hold so many components whilst working in a virtual black out until welding commences. For a few assemblies wooden jigs are fine and cost little such jigs being again very accurately put together; I prefer using wood screws for this task. A poor jig will yield poor work so the jig needs a lot of care and is well worth the time and effort to make; pictures of the wooden jig I used are shown below and the resulting railings fitted perfectly with no open badly welded joints; in this instance the jig was only used allowing face welds to be run; with the components now secured the railings could be released from the jig and welded at will; how lovely to hear the welder singing in happiness. Please be aware welding fumes build up very quickly indeed so plenty of ventilation is called for better still welding outside on a dry day if possible but I generally weld with both workshop doors wide open and quit the workshop immediately to let the air clear; I only have one pair of lungs; now the welded items are extremely hot but a novice usually finds this out quickly.
All skin in direct line with the arc needs protection; for a novice one of the auto darkening welding helmets will be a great help; mine cost £35 but I still prefer using my small shield; gloves are a must; I have big welding gloves but prefer the leather palm cheap rigger gloves but we are all different and I'm so used to using the hand shield and rigger gloves I do it without thinking. The heavy box section used on this project was welded with the 140A SIP using the usual 2.5mm electrode E6013 at around 110A; the section of this steel is 6mm and I welded caps and brackets to it with ease. Any galvanized metal (when I say metal I refer to steel) can be welded but its terrible stuff giving off lots of toxic fumes so if possible take it down to bare metal with an angle grinder before welding. As experience is gained the kit will increase to include all manner of clamps to secure work being welded but in its basic form welding is very cheap indeed and just so rewarding.
Sorry to hi-jack your thread Argyll but I'm a dinosaur who really does wish to pass on the old skills before the skills completely disappear behind a MacDonald's which people these days prefer?
I've rambled enough so here are the pictures.
Kind regards, Col.
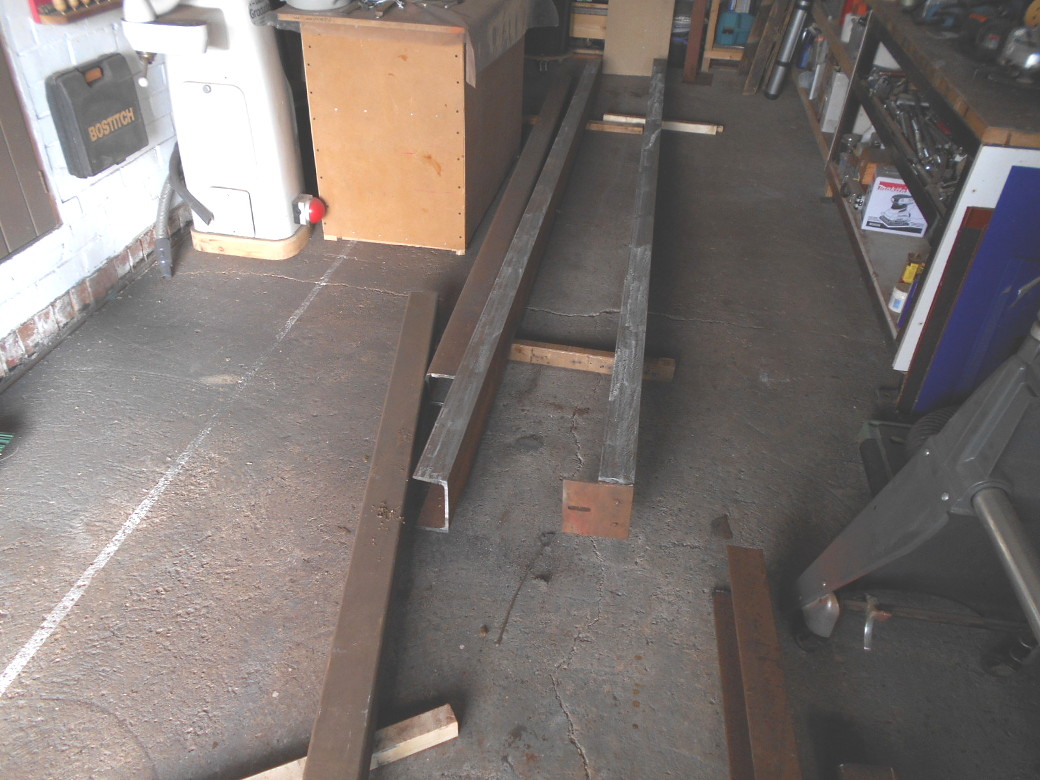
- Bungalow exterior makeover August 2016 (13).JPG (196.19 KiB) Viewed 11456 times

- Bungalow exterior makeover August 2016 (22).JPG (184.09 KiB) Viewed 11456 times

- Bungalow exterior makeover August 2016 (24).JPG (197.49 KiB) Viewed 11456 times

- Bungalow exterior makeover August 2016 (29).JPG (193.76 KiB) Viewed 11456 times
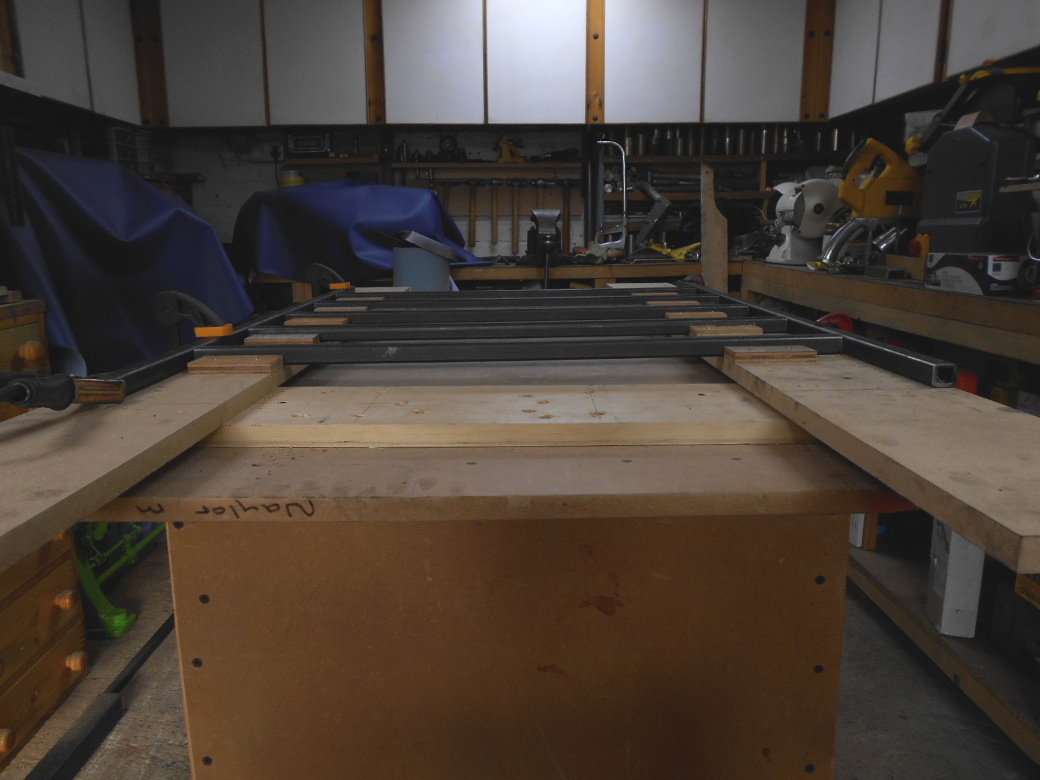
- Bungalow exterior makeover August 2016 (30).JPG (186.71 KiB) Viewed 11456 times
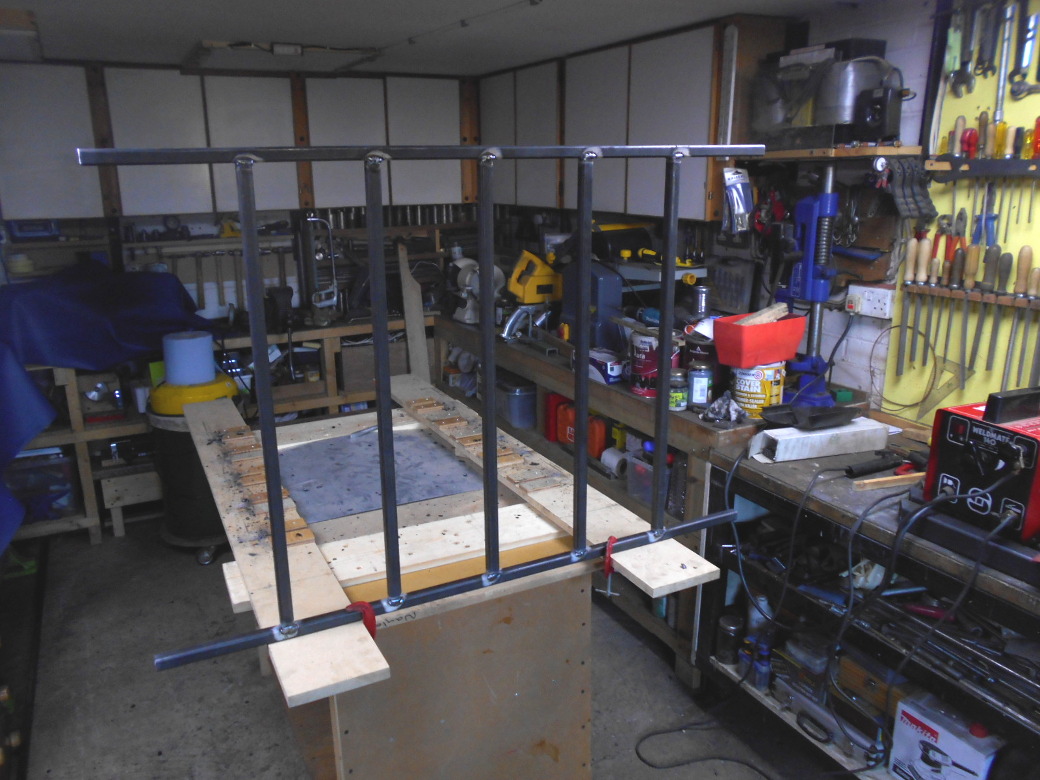
- Bungalow exterior makeover August 2016 (32).JPG (228.98 KiB) Viewed 11456 times
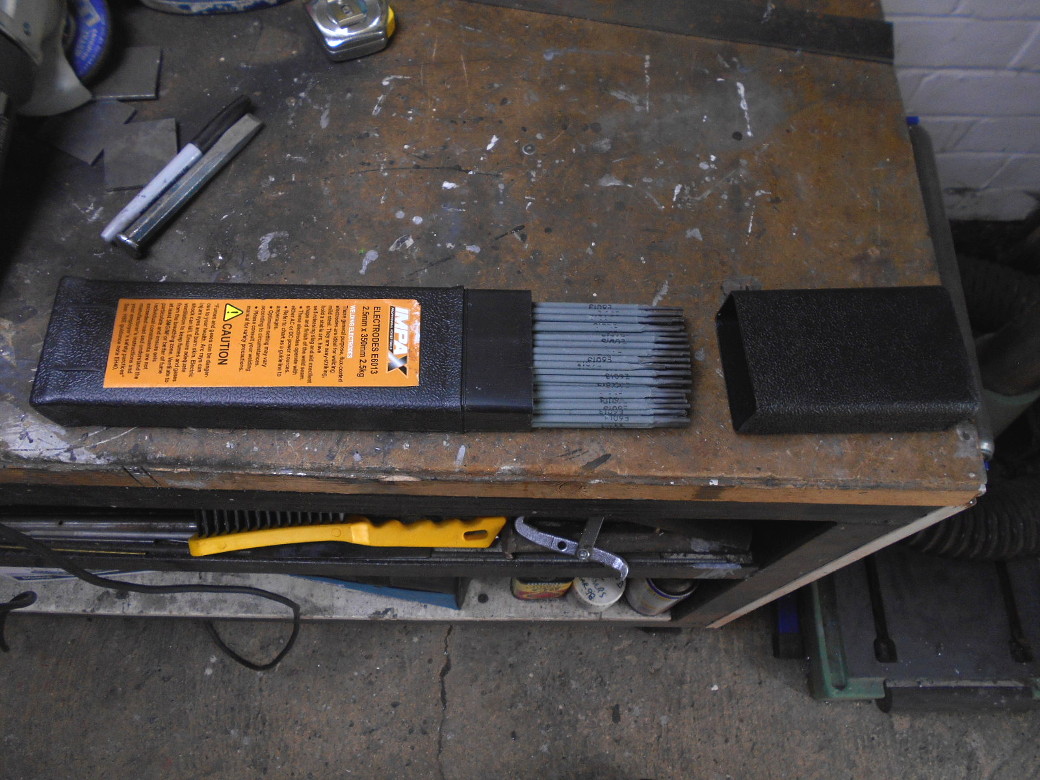
- Bungalow exterior makeover August 2016 (37).JPG (222.64 KiB) Viewed 11456 times

- Bungalow exterior makeover August 2016 (38).JPG (217.38 KiB) Viewed 11456 times
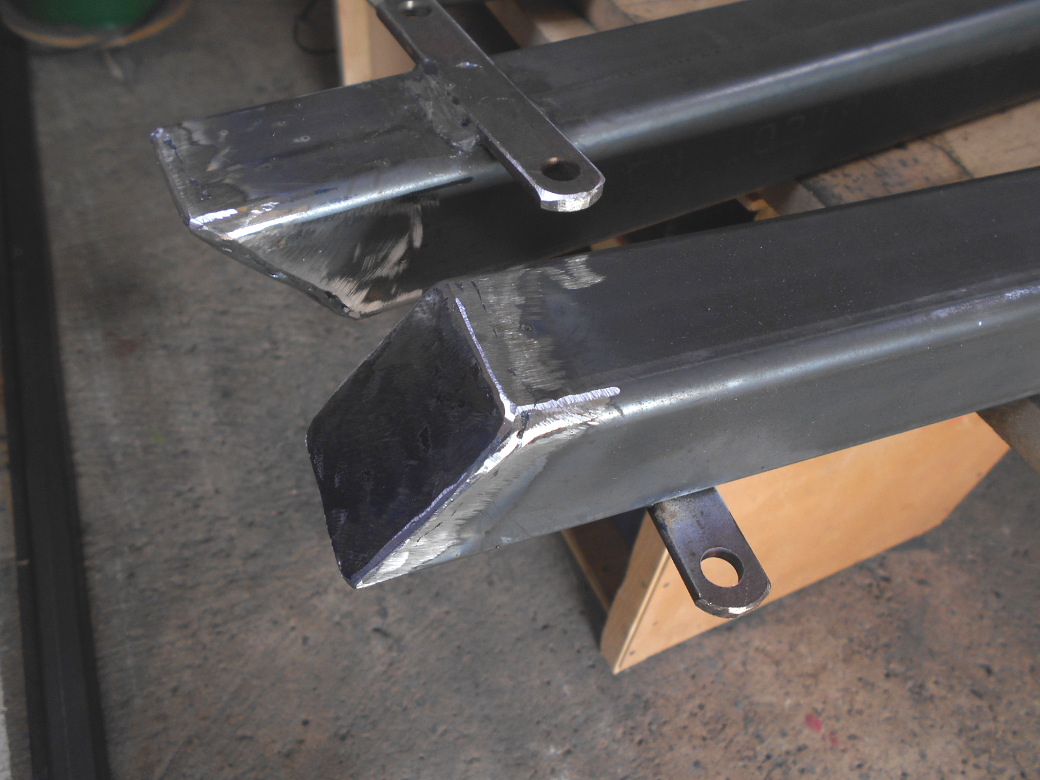
- Bungalow exterior makeover August 2016 (41).JPG (192.12 KiB) Viewed 11456 times

- Bungalow exterior makeover with new steel decking..JPG (224.87 KiB) Viewed 11456 times